IHEP Successfully Builds Silicon Module Prototype for CMS High Granularity Calorimeter
An 8-inch silicon module prototype for the compact muon solenoid (CMS) high granularity calorimeter (HGC) was successfully assembled by a team of IHEP scientists. The module has been tested at IHEP and sent to CERN for a beam test. This is the first 8-inch silicon module with the latest electronics (NSH HGCROC V2). And it is the first time a CMS HGC silicon module has been made outside of University of California at Santa Barbara (UCSB), where the HGC silicon module assembly technology was developed. IHEP has a close collaboration with UCSB, establishes the automatic production and quality control procedure, and realizes the silicon module production.
In order to fully explore physics potential on the energy frontier at the High Luminosity LHC, the CMS collaboration will replace the existing endcap calorimeter with a sampling calorimeter, which is composed of silicon and scintillators as sensitive materials. This calorimeter will operate in a hash radiation environment as high as 1016 per square centimeter 1-MeV neutron-equivalent fluence in certain region, and read out particle information approximately every 1 cubic centimeter. The information from each readout channel includes three-dimensional position, energy, and time. Thus it is also known as a 5D calorimeter. The designed energy resolution is (23-27)%/sqrt(E) and time resolution is 50 pico-second. These design targets have been verified by beam tests at CERN, Fermilab, and DESY. This novel calorimeter will be ideal for particle flow algorithms, which significantly improve jet energy resolution at the high energy experiments. The CMS HGC is the first large-scale application of this technology.
IHEP is among the first ten institutes that proposed the detector concept for HGC. According to the CMS HGC Technical Design Report, IHEP will host one of the silicon module assembly centers (MAC). Each of the six MACs across the U.S. and Asia is expected to produce an average of more than 100 m2 of silicon modules. This module uses an 8-inch silicon sensor produced by Hamamatsu in Japan and HGCROC V2 ASICs. The sensor and the front-end electronics printed circuit board are attached by epoxy. Each detecting sensor cell and its readout channel is connected by aluminum wires of 25 micrometer in diameter, which are protected by encapsulation. Quality control, module thickness, and positioning accuracy match the requirement of HGC. Electronics tests show that it functions properly. The noise performance is as expected.
After the producing of this first HGC silicon module, IHEP will prepare for a site qualification over the next few months, followed by pre-production and official production for the CMS collaboration. The full HGC detector is expected to operate and take physics data in 2027. The project is sponsored by MoST, NSFC, and IHEP.
Fig. 1. A first 8-inch HGC silicon module produced at IHEP (left). Noise map of this module in unit of ADC counts (middle). Comparison of the noise before and after assembly, where the red and blue dots are for noise before and after assembly, respectively (right).
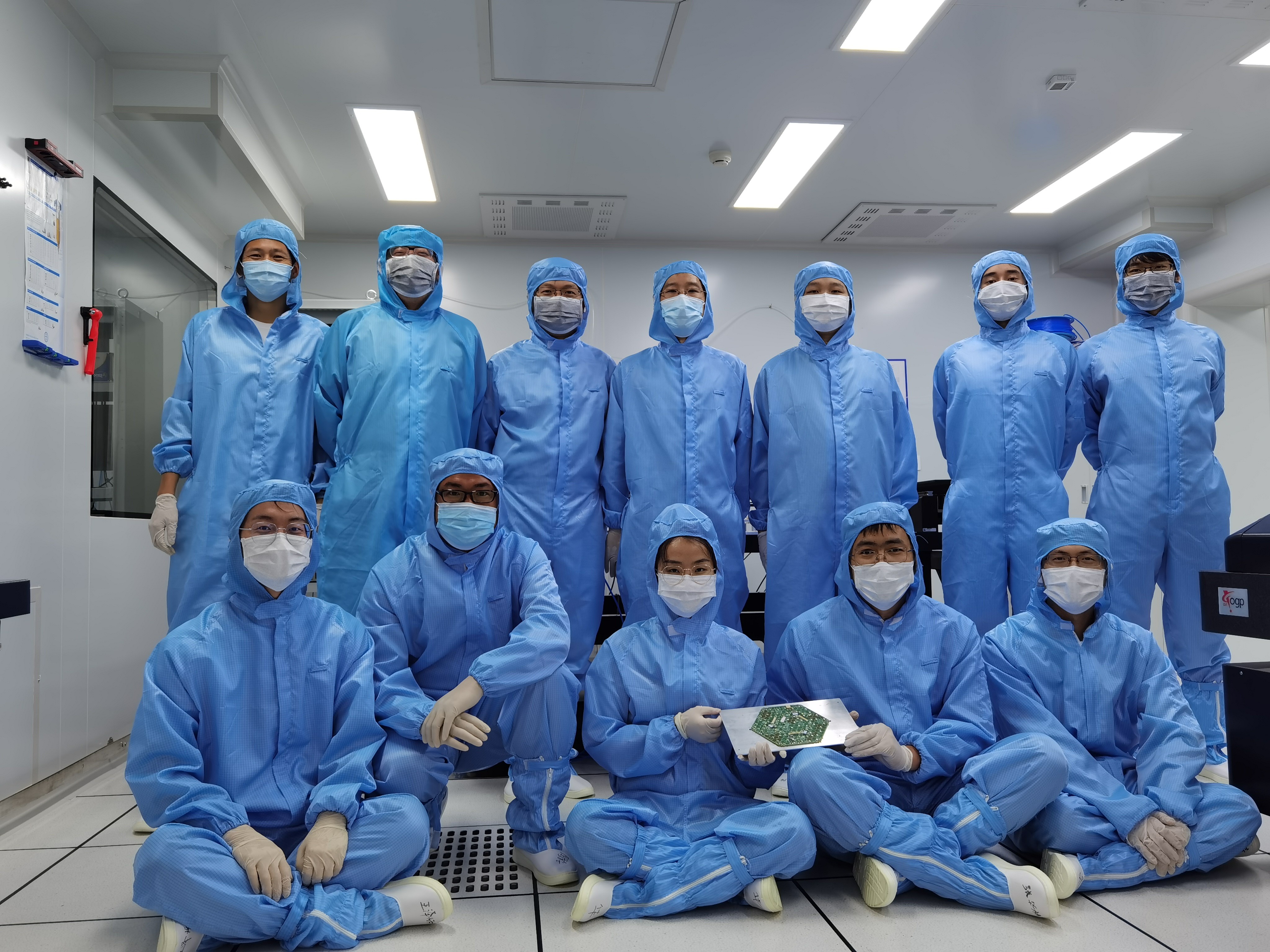
Contact Information
Mr. GUO Lijun
ljguo@ihep.ac.cn